Dressing And Trueing
Grinding Support
Safety
Miscellaneous Information
Information on fixed abrasives
- Catalog Download
- List of Catalog Download
- Grinding & Polishing Technical Information "NORITAKE TECHNICAL JOURNAL"
- About Our Sales Offices
Dressing And Trueing

Dressing
When the sharpness of grinding wheel becomes dull because of glazing and loading, dulled grains and chips are removed (crushed or fallen) with a proper dressing tool to make sharp cutting edges and simultaneously, make recesses for chips by properly extruding to grain cutting edges. Thus, these operations are for the dressing.
Trueing
When the grinding wheel is mounted to the grinding wheel spindle, the run-out on wheel operating surface is removed, the wheel during contour grinding is trued or worn grinding wheel is corrected. Thus, these operations are for the trueing.
Table of Dresser Uses by Grinding Tool
T: trueing; D: dressing; ◎: used; ○: can be used; △: is sometimes used
Dresser type | Diamond wheel | CBN wheel | Conventional wheel |
||||||||||||||
---|---|---|---|---|---|---|---|---|---|---|---|---|---|---|---|---|---|
Vitrified | Resinoid | Metal | Plated | Vitrified | Resinoid | Metal | Plated | ||||||||||
T | D | T | D | T | D | T | D | T | D | T | D | T | D | T | D | D | |
Single-point | ◎ | ○ | ◎ | ||||||||||||||
Multi-point | ◎ | ◎ | ○ | ◎ | |||||||||||||
Impregnated | △ | △ | ◎ | ○ | ◎ | ◎ | |||||||||||
Cap rotary | △ | ◎ | ○ | △ | |||||||||||||
Rotary | ◎ | ◎ | ◎ | ○ | ○ | ◎ | ◎ | ◎ | ○ | ○ | ◎ | ||||||
Vitrified diamond wheel | ○ | ○ | ◎ | ◎ | ◎ | ◎ | |||||||||||
Resinoid diamond wheel | ○ | ◎ | ◎ | ||||||||||||||
Metal diamond wheel | ◎ | ◎ | ◎ | ◎ | ◎ | ◎ | |||||||||||
plated diamond wheel | ◎ | ◎ | ◎ | ◎ | |||||||||||||
Diamond roller | ◎ | ◎ | ◎ | ◎ | |||||||||||||
Diamond block | ◎ | ◎ | ◎ | ◎ | ◎ | ||||||||||||
Wheel block grinder | ◎ | ◎ | ○ | ○ | ◎ | ◎ | ○ | ○ | |||||||||
Wheel brake control | ◎ | ○ | ◎ | ○ | ◎ | ○ | ◎ | ◎ | ◎ | ◎ | ◎ | ○ | |||||
Wheel roller drive | ◎ | ◎ | ○ | ○ | ◎ | ◎ | ○ | ○ | |||||||||
Wheel stick push | ○ | ◎ | ○ | ◎ | ◎ | ◎ | ○ | ||||||||||
Mild steel grinder | △ | ○ | ◎ | △ | ○ | ◎ | |||||||||||
Metal crusher | ◎ | ◎ | ◎ | ◎ | |||||||||||||
Metal wire brush | ◎ | ◎ | |||||||||||||||
Crushing roller | ◎ | ○ | ◎ | ○ | ◎ | ||||||||||||
Abrasive lapping | ○ | ◎ | ○ | ◎ | ○ | ◎ | ○ | ◎ | ○ | ◎ | ○ | ◎ | |||||
Abrasive jet | △ | ○ | △ | △ | ○ | △ | |||||||||||
Abrasive sludge pouring | ○ | ○ | △ | ○ | ○ | ||||||||||||
Wire electrode discharge | ◎ | ◎ | ◎ | ◎ | |||||||||||||
Electrolysis | ◎ | ◎ |
Main dressing and sub-trueing tool
One diamond is mounted to the shank in various methods. Size is indicated at weight (carat … ct), the units of 1/4, 1/3, 1/2, 3/4, 1, 2, 2.5, 3ct, etc. are usually used (1ct = 0.2g).
There are diamond shapes such as normal type and pyramid, cone, wedge types reshaped for profile grinding.
Single-point forming diamond dresser
Normal type

Natural diamond is used by extruding the edge of rough stone as is. This type is used for general grinding.
Pyramid type (point dresser)

The rough diamond is formed to quadrangular pyramid. This type is for precision grinding to use the sharp edge.
Cone type (point dresser)

Rough diamond is formed to the cone type and its tip cutting edge is used for the precision thread grinding, gear grinding, etc.
Wedge type (forming dresser)

One diamond polished to shape and sizes matched to used tool is embedded for precision form grinding.
Reishauer dressers

The diamonds of Resihaur dressers are ground to be flat and parallel with the shank.
Resihauer dressers are used to shape wheels for gear grinders.
(Origin of name: these dressers are used with the grinding machines made by Reishauer AG.)
Multi-point types
Multi-point diamond dresser

Two to tens of diamond are embedded in this dresser. It is called what piece what step by the number of diamonds on surface and the number of steps on layer. Since the diamonds of this dresser are hardly damaged, even operator who is not expert, it can be easily used.
Blade type multi-point diamond dresser

Some diamonds are arranged in a line or layered. Two or more of diamonds are continually used so as to be contacted. This type is economical since it can be used to the end without correction. It is also used for form grinding.
Impregnated diamond dresser

The diamond powers (#60 ~ #400) are sintered with high wear resistance metal. This dresser is used for the grinding wheel of precise grinding.
Bond diamond dresser (grid dresser)

The infinitesimal grains (#16 ~ #40) of diamond are sintered with high wear resistance metal. This dresser is suitable to a large type grinding wheel like the centerless grinding wheel.
Detailed single point diamond dresser
Grinding performance is influenced by the conditions of dressing and trueing. If the rigidity of dresser is small and the dresser is incorrectly mounted, correct dressing is impossible. The diamond dresser is usually tilted to 15°of angle. When set less than this angle, the finished surface becomes wrong.
How to mount single point diamond dresser correctly
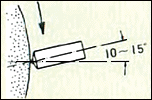
The grinding wheel is mounted at 10 ~ 15°of angle for horizontal face of wheel.
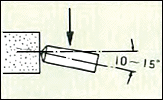
The grinding wheel is mounted at 10 ~15°of angle for circumference of wheel.

The effect that feed speed, cut depth and mounting angle of the dresser have on finished surface roughness is shown in the graph. As the mounting angle gets wider the finished surface roughness gets smoother.
Feedrate of dresser
As the feedrate increases, the cutting blade gap grows wider and the sharpness of the wheel increases but machining precision gets worse. Conversely, as speed decreases, machining precision improves but it becomes more prone to clogging and cutting ability decreases. One guide with the dresser feedrate is to go over every grain 2 to 3 times, which can be determined with the following equation.
F = (d×N)/2.5
F: Dresser feedrate (mm/min)
d: Average grain diameter (mm)
N: Wheel rotation count (1/min)
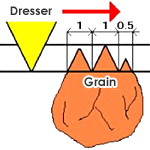
Granularity | F46 | F54 | F60 | F80 | F100 | F120 | F150 |
Average grain diameter | 0.4 | 0.3 | 0.25 | 0.18 |
0.13 |
0.10 | 0.07 |
Depth of Cut and Total Depth of Cut
The effect of depth of cut on grinding performance is not large enough to impact the feed speed, but the fractured state of the grain can change, so it is related to finished surface roughness.
A small depth of cut with a radius of about 5 μm should be set for precision grinding due to the production of minute fractures in the grain.
For general grinding, the depth of cut is set to a radius of about 10 – 30 μm in order to break down the grain properly.
For rough grinding, a depth of cut radius can be set to about 40 μm, which partially breaks down the bond bridge, widening the grain spacing and greatly increasing the amount of material removed.
On the other hand, the total cut depth can change the wear and clogging of the grain. Performance cannot be improved or restored when the total depth of cut is not sufficient, and excess depth of cut can invite insufficient grain protrusion. For a general grain, one guide should be 10 – 30% of grain diameter, and it is recommended that you check whether the prescribed performance (finished surface roughness, dress gap, etc.) has been restored or improved.
How to select diamond size
The diamond size is determined by grain, grain size, grade, bond and sizes (diameter × thickness) and it is selected as follows.
Abrasive grain: | C-system more than A-system is | ……………….large. |
Grain size: | Rough grain more than fine grain is | ……………….large. |
Hardness: | Hard diamond more than soft diamond is | ……………….large. |
Bond: | Organic more than minerals is | ……………….large. |
Grinding wheel diameter: | Large diameter is | ……………….large. |
Grinding wheel thickness: | Large thickness is | ……………….large. |
Trouble by dressing failure and it’s troubleshooting
Problems that arise during dressing are directly connected to grinding problems. In order to get sufficient performance from wheels, dressing must be correctly carried out.
Items related to dressing that can be checked in order to prevent defects from arising during grinding are given below.
Condition | Troubleshooting |
---|---|
Irregular chatter | • Use sharp diamond dresser. • Replace tip-flatted dresser with new one. • Check diamonds are securely held. • Check dresser shank is not excessively protruded. |
Scratch (Fine threading mark) | • Check diamond is not broken. • Reduce diamond feed. • Mount diamond dresser downward 15°. • Mount holder securely. • Reduce depth of cut for dresser and feed dresser several times at infeed amount. • Be sure to dress from grinding wheel edge. • Feed dresser finally in reverse direction as grinding feed. • Feed dresser uniformly. • Round end faces of grinding wheel. |
Feed mark | • Reduce infeed amount and feed for dresser. |
Irregular flaw | • Use sharp diamond dresser. • Brush grinding wheel after dressing. |
Large consumption of wheel | • Reduce depth of cut and increase feed. |
Loading of grinding wheel | • Use sharp diamond dresser. • Increase dresser feed. • Clean surface after dressing. |
Glazing of grinding wheel | • Increase dressing times with sharp diamond dresser. • Increase infeed amount and feed of dresser. |
Roundness failure of workpiece | • Check wheel operating surface is not loaded or glazed. • Match dressing position and grinding position. |
Workpiece tapered | • Approach diamond dresser to grinding position. |
Burn marks, braking | • Increase dresser feed and dressing times. |