PRODUCTS
Ceramic cores for precision casting
Ceramics & Materials
- Electronic Paste (Thick Film)
- Gypsum
-
Engineering Ceramics
- Engineering Ceramics List
- Ceramic cores for precision casting
- Porous ceramic component
- Decoration Materials
- Electronic Ceramic Powder
- Vacuum Fluorescent Display
- Thick Film Circuit Substrate
- Dental Materials
- Technical Support
- Technical Support List
- What is decalcomania?
- Thick Film Circuit Substrate with Precious Metal design guidance
- About Our Technology
- New Copper Conductors + Plating Substrate design guidance
- Thick Film Circuit Substrate with Copper Conductors design guidance
- Thick Film Heater design guidance
- Catalog Lineup
- Pore size control for porous ceramic components
- Core Material Characteristics
- ℃ MONARC Characteristics
- Catalog Download
- About Our Sales Offices
Technical Support
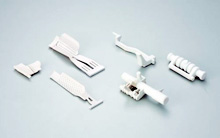
-
NORITAKE's ceramic cores for precision casting offer excellent stability at high temperatures. Used for manufacturing high-precision moving blades and stationary ones for gas turbines and jet engines, these ceramic cores contribute greatly to engine efficiency. They also allow assembling by jointing in manufacturing complex-shaped objects like cores for pump impellers.
NEW PRODUCT Medium-pressure Injection Molded Ceramic Cores
Features
- Variety of Size and Shape
We have various molding methods and materials, and we can support any sizes and shapes of the products. - Accuracy and Appearance
Our products contribute to qualiy improvement of castings due to excellent dimensional accuracy and visual appearance. - Superior Leachability.
Steady rate of pores allows superior leachability.
Ceramic core manufacturing processes

Core material characteristics
Material model | N-200 | ℃ MONARC NEW | N600 | N700 | ||
---|---|---|---|---|---|---|
N400 | N450 | N500 | ||||
Major composition | SiO2-ZrSiO4 | SiO2-ZrSiO4 | SiO2-ZrSiO4-Al2O3 | SiO2-Al2O3 | SiO2-Al2O3 | SiO2-ZrSiO4 |
Molding method | Pouring method | Method-pressure injection molding | High-pressure injection molding | |||
Shirinkage rate |
0.2% | 1.0% | 1.0% | 1.0% | 0.9% | 1.6% |
Trace impurities(ppm) | ||||||
Fe | <300 | <80 | <80 | <30 | <200 | <300 |
Pb | <25 | <25 | <25 | <25 | <25 | <25 |
Bi | <1 | <1 | <1 | <1 | <1 | <1 |
Ag | <1 | <1 | <1 | <1 | <1 | <1 |
Characteristic values | ||||||
Porosity(%) | 30 | 34 | 33 | 34 | 35 | 34 |
Thermal expansion rate(%) at 1,000℃ | 0.25 | 0.25 | 0.25 | 0.25 | 0.10 | 0.25 |
Bending strength(Mpa) | ||||||
at RT | 7 | 6 | 9 | 10 | 7 | 8 |
at 1,000℃ | 24 | 20 | 25 | 24 | 20 | 22 |
Size(mm) | ||||||
Maximum length | ~L1000 | ~L500 | ~L300 | ~L250 | ||
Minimum length | 0.80 | 0.50 | 0.50 | 0.30 | ||
Cast type | CC/DS/SC | CC | CC/DS/SC | CC | CC/DS/SC |
※左右にフリックすると表がスライドします
Selection is made from among the above materials on the basis of the molten metal temperature, casting materials, and shape (size) of the cast product at customer’s request.