- HOME
- Product Information
- Engineering
- Filtration Systems
- Ceramic filter
- Ceramic filter For Chemistry
Ceramic filter For Chemistry
Engineering
-
Heating Furnaces / Kilns
- Heating Furnaces / Kilns List
-
Drying Furnace
- Drying Furnace List
- Batch Kiln
- Far Infrared Conveyer Furnace
- Other Drying Furnaces
- Roll to Roll Far-infrared Heating Furnace
- Far Infrared Heater
-
Firing Kiln
- Firing Kiln List
- Roller Hearth Kiln
- Pusher Kiln
- Rotary Kiln
- Other
- Batch Kiln
- Refractory
-
Search by industry or usage
- Search by industry or usage List
- Semiconductors
- Energy
- Electronics
- Automobiles
- Displays and lighting
- Other
- Furnace Construction Maintenance
-
Mixing Technology
- Mixing Technology List
-
SM Engineering Equipment
- SM Engineering Equipment List
-
Heating and Cooling Systems
- Heating and Cooling Systems List
- Saccharification system for bio-ethanol production
- Adhesive Temperature Adjusting System
- Coating Liquid Precision Temperature (viscosity) Adjusting System
- Scrambled Eggs Continuation Manufacturing System
- Condiment Miso Heat Sterilization System
- Starch Gelatinization System for Paper Manufacturing
- Flour Paste Manufacturing System
- PVA Continuous Dissolution System
- Seasoning Liquid Heating Sterilization Cooling System
- Automated Oxidized Starch Production System
- In-line Starch Saccharification System
- Water Heating System
- Mixing Systems
- Powder and Liquid Dispersion System
- Reaction System
- Laboratory Test Systems
-
Heat Exchangers
- Heat Exchangers List
- Heat Exchangers
- Reaction
-
Static Mixer (SM)
- Static Mixer (SM) List
- Gas absorption(Option)
- Homogenization
- Miixing
- Option Parts
- Search by industry or usage
- Cooker / Steam Mixer
- Cutting Machine (Thin Cut Master : TCM)
-
Filtration Systems
- Filtration Systems List
- Search lubricants
-
Coolant Filtration Systems
- Coolant Filtration Systems List
- Centrifuge
- Coolant Tank Unit
- Magnetic Separator
- Cyclone Separator
- Paper Filter
- Backwash Filter
- Centralized Filtration Systems
- Search filtration materials
- Filtration Related Systems
- Ceramic filter
- Technical Support
- Catalog Download
- About Our Sales Offices
Technical Support
High-purity purification of slurries and polymers!
Features
High precision filtration
High filtration accuracy is obtained because the pore size distribution is uniform and sharp.
Corrosion resistance
The filter element made of alumina ceramics, which has excellent corrosion resistance, can be used for a wide range of solvents and chemicals by combining it with a casing with a Teflon lining.
Stable layer operability
There is no opening or damage to the filter while the line is in operation, making operation management easier.
Renewable resource
It is possible to regenerate the filter that has been used for a long time by cleaning it with chemicals and firing it.
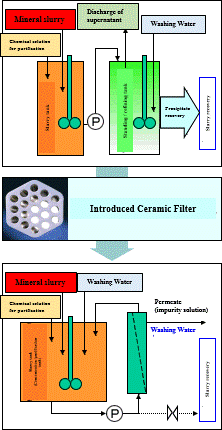
Delivery example
Advantages of delivering ceramic filters (see the upper right figure)
(1) Space saving is possible because there is no need for a stationary / refining tank.
(2) Since purification, concentration, cleaning, etc. can be performed in the slurry tank, the work process can be simplified.
(3) By forced separation with a filter, the time required for slurry sedimentation in the static / purification tank can be shortened.
Main application
- Concentrated recovery and purification of slurry paste
- Separation and purification of polymers and monomers
- Purification of chemicals
- Removal of emulsion particles
Example
What is diafiltration! !?
This is a method in which the same amount of liquid (solvent) as the amount of permeated liquid is added to the stock solution tank to continuously permeate low molecular weight substances through the membrane. The main purposes are high-purity purification of polymer substances, desalination, desalination, pure water substitution, solvent substitution, etc., and processing that meets the needs has become possible.
The graph on the right shows the polymer purification data. Impurity concentration decreases as DF filtration (diafiltration) progresses. At DF magnification (2x), the impurity concentration drops to about 1/5. Even in this case, the recovery rate of valuable components can be maintained high.
