- HOME
- Product Information
- Engineering
- Filtration Systems
- Filtration Related Systems
- Sludge Solidification Machines
Sludge Solidification Machines
Engineering
-
Heating Furnaces / Kilns
- Heating Furnaces / Kilns List
-
Drying Furnace
- Drying Furnace List
- Batch Kiln
- Far Infrared Conveyer Furnace
- Other Drying Furnaces
- Roll to Roll Far-infrared Heating Furnace
- Far Infrared Heater
-
Firing Kiln
- Firing Kiln List
- Roller Hearth Kiln
- Pusher Kiln
- Rotary Kiln
- Other
- Batch Kiln
- Refractory
-
Search by industry or usage
- Search by industry or usage List
- Semiconductors
- Energy
- Electronics
- Automobiles
- Displays and lighting
- Other
- Furnace Construction Maintenance
-
Mixing Technology
- Mixing Technology List
-
SM Engineering Equipment
- SM Engineering Equipment List
-
Heating and Cooling Systems
- Heating and Cooling Systems List
- Saccharification system for bio-ethanol production
- Adhesive Temperature Adjusting System
- Coating Liquid Precision Temperature (viscosity) Adjusting System
- Scrambled Eggs Continuation Manufacturing System
- Condiment Miso Heat Sterilization System
- Starch Gelatinization System for Paper Manufacturing
- Flour Paste Manufacturing System
- PVA Continuous Dissolution System
- Seasoning Liquid Heating Sterilization Cooling System
- Automated Oxidized Starch Production System
- In-line Starch Saccharification System
- Water Heating System
- Mixing Systems
- Powder and Liquid Dispersion System
- Reaction System
- Laboratory Test Systems
-
Heat Exchangers
- Heat Exchangers List
- Heat Exchangers
- Reaction
-
Static Mixer (SM)
- Static Mixer (SM) List
- Gas absorption(Option)
- Homogenization
- Miixing
- Option Parts
- Search by industry or usage
- Cooker / Steam Mixer
- Cutting Machine (Thin Cut Master : TCM)
-
Filtration Systems
- Filtration Systems List
- Search lubricants
-
Coolant Filtration Systems
- Coolant Filtration Systems List
- Centrifuge
- Coolant Tank Unit
- Magnetic Separator
- Cyclone Separator
- Paper Filter
- Backwash Filter
- Centralized Filtration Systems
- Search filtration materials
- Filtration Related Systems
- Ceramic filter
- Technical Support
- Catalog Download
- About Our Sales Offices
Business Overview
With the growing awareness for global environmental conservation these days, there is an increasing focus on efforts by business to accommodate the creation of a recycle-oriented society. Our company currently manufactures and sells grinding sludge solidification machines that enable materials that result from the solidification of grinding sludge (after removal of water and oil) to be recycled as raw materials rather than being mainly processed as industrial waste for landfill disposal. We also aim to construct the recycling systems that are indispensible for recycling solidified sludge (briquettes).
In order to develop solidification machines, we’ve drawn on the strengths of NTN Corporation, applying techniques developed through high-volume testing. We have created commercial products through ground-breaking technology that is capable of solidifying grinding sludge without the use of hardening agents so that the coolant can be reused and the resulting briquettes can be recycled.
Going forward, our company will continue to engage in productive research and development for recycling industrial waste produced from grinding processes, to develop unique products that are useful for reducing the environmental impact, and to contribute by achieving zero emissions.
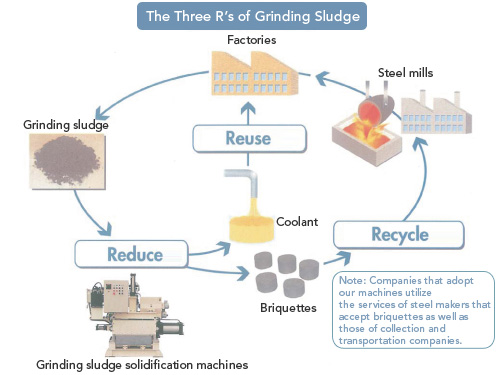
What is a grinding sludge solidification machine?
The sludge discharged during the grinding process contains moisture or oils used as a coolant, and both transport and waste disposal of this sludge are extremely difficult. A grinding sludge solidification machine efficiently compresses the sludge, thereby reducing weight and volume.
It also converts the solidified sludge into a briquette form facilitating subsequent handling.
Features
Volume reduced from one-third to one-fifth of original sludge (weight reduced about three-fifths).
The majority grinding sludge volume consists of coolant.
The proportion accounted for by coolant is reduced to 10% or less through solidification.
Coolant recovery rate: 90% or more
Coolant discharged during solidification can be reused.
These machines can handle a wide variety of grinding sludge.
These machines include a unique compression and dehydration device that enables them to accommodate the grinding sludge produced during the machining processes for producing bearings and automotive components. (See diagram at right.)
Compression and dehydration device
A suitable speed can be chosen for when grinding sludge is compressed.
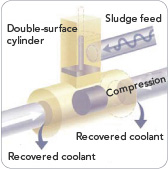
Cost Reduction Through Grinding Sludge Solidification
- Reduction in waste processing costs
Processing costs can be reduced by reducing the amount of grinding sludge produced.
Cost reduction = discharge amount × processing fee × (approx. 50%) - Coolant reuse
Coolant can be reused through a simple filtration device.
Cost reduction = discharge amount × (approx. 50%) × (coolant cost) - Total cost reduction
Total cost reduction = waste processing cost (1) × coolant cost (2)
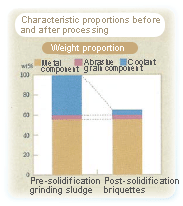
Model-Specific Specifications
PRG-I (100 t) Machine Specification
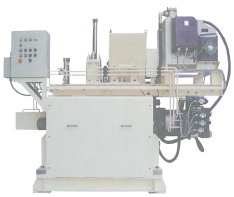
Processing capacity* (kg/h) |
(water-soluble sludge) up to 80 (oil-soluble sludge) up to 40 |
---|---|
Water/oil removal amount (% by weight) |
90% or more |
Compression capacity (kN) |
max. 1010 |
Briquette diameter (mm) |
Φ70 |
Compression surface pressure (MPa) |
Up to 263 (theoretical value) |
Hopper capacity (L) | 50 |
Total power capacity (kVA) |
10 |
Rough dimensions (L × W × H mm) |
Approx. 2,510 × 850 × 2,200 |
*Processing capacity may vary according to the state of the sludge.